A little Something on Custom One Off Vinyl Records, Mastering & Pressing
- Byron
- Apr 8, 2018
- 9 min read
Lathe cut vinyl a relatively new way of producing a one off vinyl record that is very different to the traditional method of transferring audio to vinyl master discs; you cannot replicate a custom vinyl record it is not a master disc. All records are individually cut on lathe cuts and mastered in real-time.
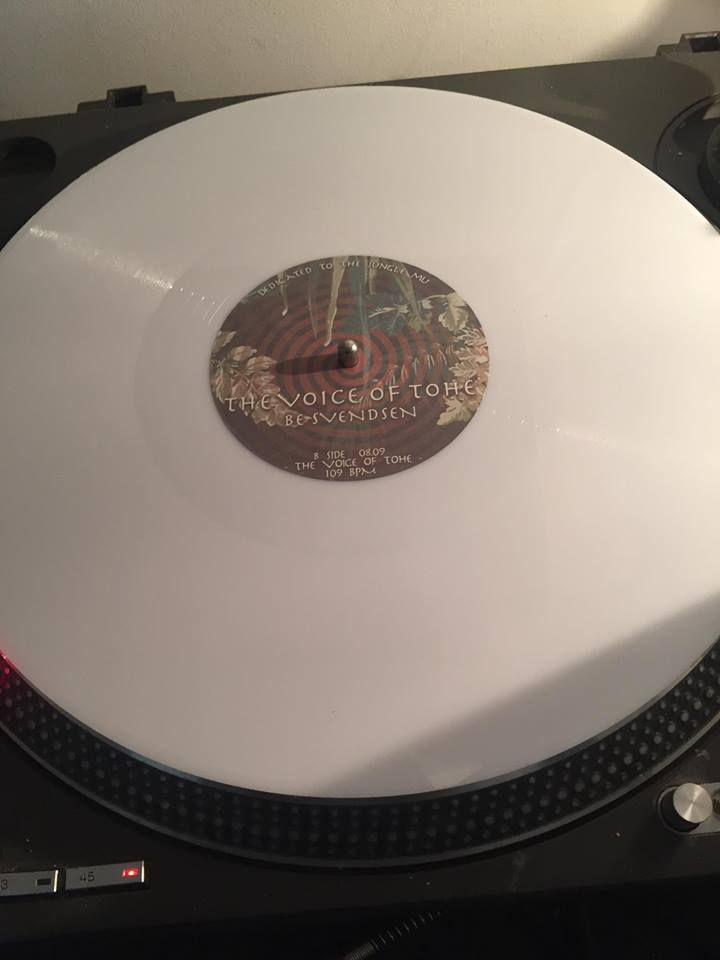
A lathe cut vinyl record gives the client the opportunity of having their music cut onto vinyl instantly without having to wait many months for the finished product to be pressed at the pressing plant.
We produce Stereo Lathe cut records at Byron's Yard by spraying the polycarbonate blank with an antistatic solution, to allow the chip that is cut out of the groove to be removed by the vacuum suction and to reduce background noise. The chip removal of a lathe cut record is much more difficult than with cutting a lacquer master or dubplate. We cut the records on the Scully vinyl mastering lathe that's fitted with the Vinylium pitch 98 pitch controller.
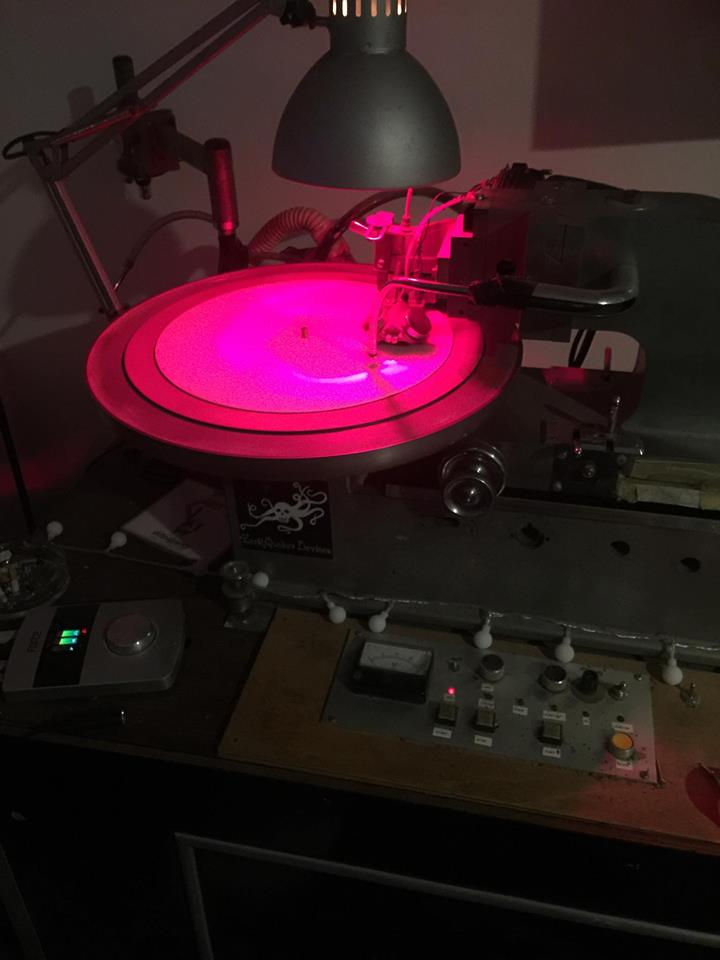
The audio is sent to the Vinylium SC99 cutter head housing the diamond styli from the Vinylium VC200 cutting amplifier, which in turn supplies Logic Pro and focus-rite Forte DAW.
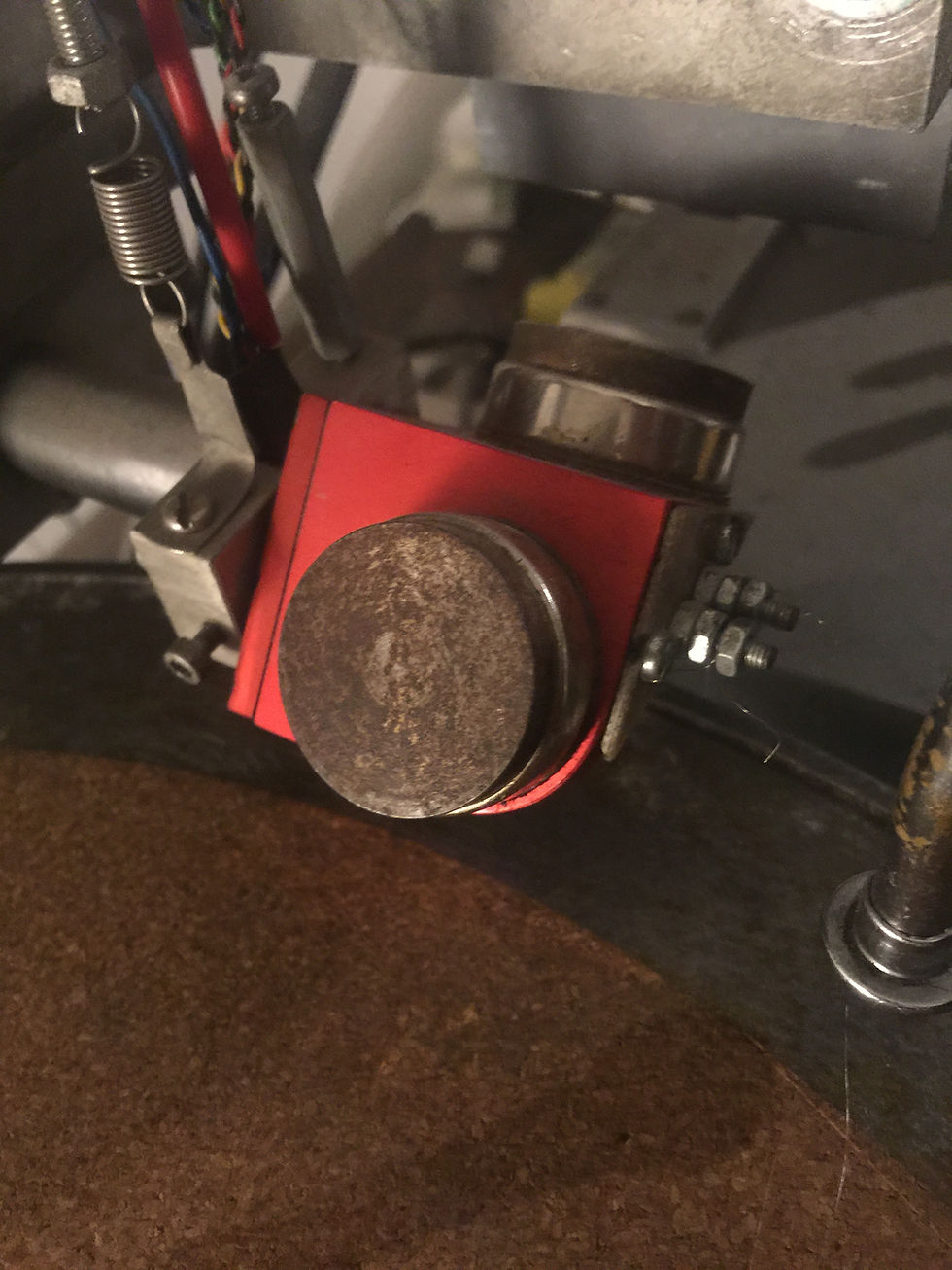
The diamond stylus has to be heated, also to eliminate background noise from the disc when creating a custom vinyl record. The other main difference between conventional vinyl lacquer mastering is the use of a diamond Styli instead of a Sapphire or Ruby as used in the lacquer mastering process.
Our lathe cuts are in black, clear or white transparent polycarbonate discs that have been routed and cut on a CNC machine. The blanks are thicker than standard records and match the weight of heavyweight factory produced vinyl record pressings.
We require a WAV file to be supplied for mastering the track or tracks though we can cut from mp3. And can work with sample rates up to 96k in either 16 or 24bit, the better the audio quality we receive, the better the results.
Preparing Songs For Cutting To Vinyl Record
Some rules to follow when preparing your audio for Short-Run record cuting polycarbonate disc or to acetate master disc. It is essential to keep all bass frequencies below 500hz mono and use any stereo widening effects above 500hz as these can cause the cutting styli to jump and ruin the cut as well as the somewhat expensive cutting styli.
Be very careful with the high freqs like cymbals and hi-hats as they distort severely on record, and should not be boosted above 10k look to gain more brightness boosting a bit lower than 7k.
Sibilance
Excessive sibilance is another problem when mastering for vinyl sibilant sounds distort terribly and limit the level that we can cut the record at and also requires the use of a deesser to be used just to make the record cuttable without destroying the lathe cutter head.
So as well as a loss of volume on your vinyl master there is a loss of high-frequency content. To enable the record to be cut sibilance should be dealt with in the mixing process either by riding the faders or by using compression.
Sibilance: High levels of sibilance will mean the use f the de-esser filter. The de-esser filters are in the 5-8khz range, and therefore rather than only de-essing the vocal tracks, everything in that frequency range will be changed this along with volume reduction is what has to be done to eliminate or reduce this distortion.
This compression reacts only to the problem-frequencies. It is fast and easy to tweak and find the problem, but it can make your vocal sound boxy and pull down other syllables if applied too harshly.
Overly Limiting or even limiting at all is not necessary for vinyl mastering dynamics is king! We can still cut your record from limited files, but will have to cut a quieter vinyl master, and your recording is also closer to the noise floor. Any noise or hiss will be more pronounced or noticeable especially when cutting longer sides.
Another thing to plan is the track listing. Although this advice only really applies to ep and albums. The high freqs fall off the closer you get to the center of the record, more audio data needs to fit into a smaller space. You can eq the inner tracks a little more brightly to compensate for this
When listening to lp’s have you noticed that the softer or quieter songs are nearer the center of the record? And the stand out tracks towards the edge? All off this should go into your thinking when you are planning out your vinyl production.
Total Audio Length for 7″ and 12″ records
12″
45rpm 9 mins per side
33rpm 1519 mins per side
7″
45rpm 4mins per side
33rpm 6 mins per side
Dubplate Cutting And Acetate Masters
Producing an acetate master or cutting a dubplate is the next stage, the dubplate is usually used to test the sound on club systems.
The acetate is an intermediate stage before the production of the master disc and is used for test purposes to assess the sound transfer from the master tapes to vinyl. If a sound or mix is rejected, then the acetate pressed is a unique item as there are never many copies of acetates produced, usually no more than 10 and are highly sought after.
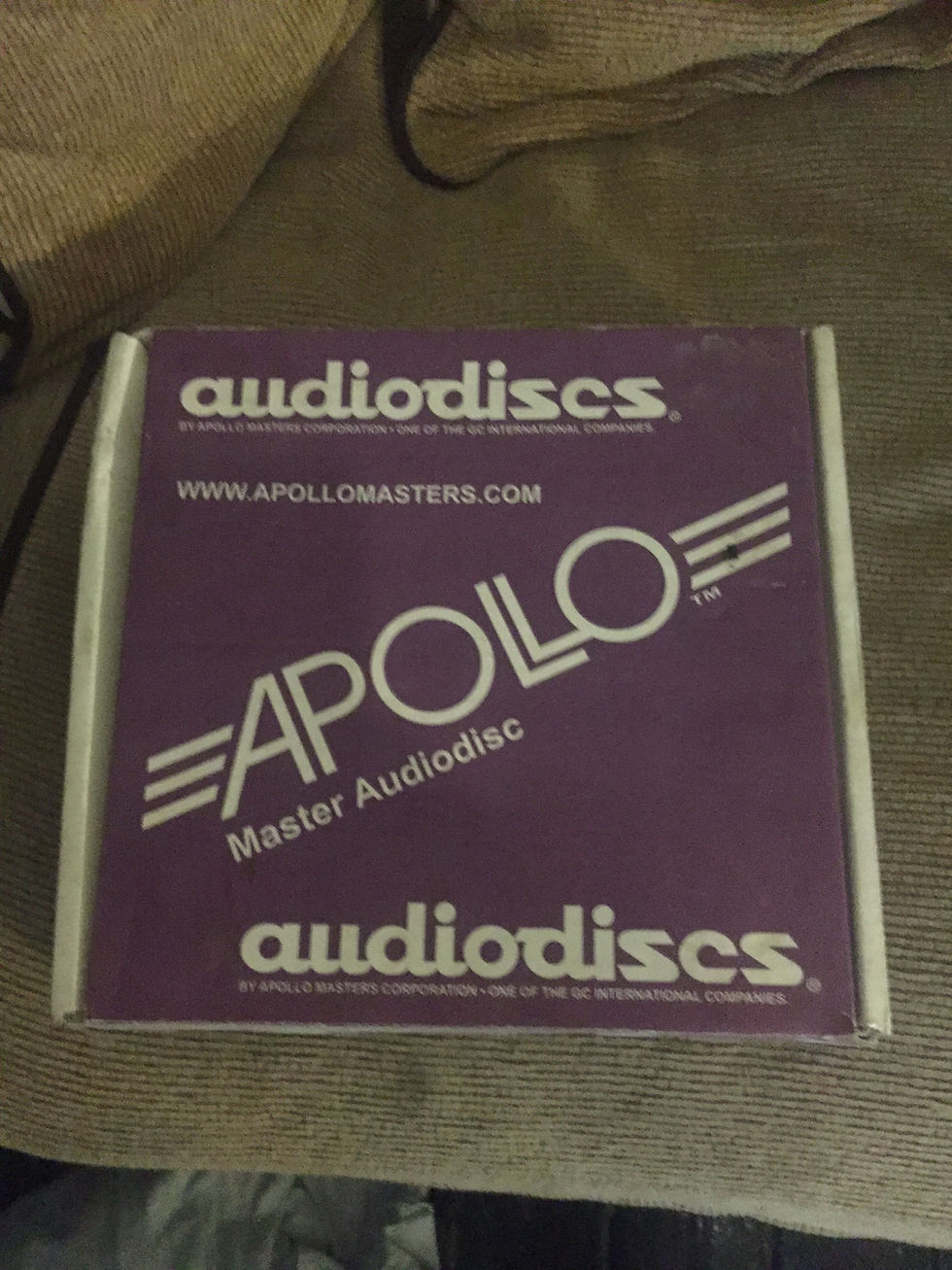
The acetate is an aluminum disc covered with a thin coating of nitrocellulose lacquer that has the sound groove, from the master tape, cut into it using a "lathe."
They come in various sizes including 10", 12" and 14."
The lacquer disc is soft and thin and repeated playing of the acetate will degrade the sound. Lacquers are produced for quality control and not continuous playing.
There are two types of acetate single-sided and double-sided discs. For single-sided discs when the mastering is complete, there will be two acetates to take away, one for the "A" side and another for the "B" side.
On the back of these singles, there are two peg holes, the center one as with regular records to place on the turntable and the offset one. This second peg hole is for turning the disc on the lathe to stop the disc slipping.
There are two discs used in the vinyl record mastering process as you cannot proceed to the next step with a double-sided acetate.

Double sided discs are reference discs given to band members or record companies, but are also well loved by DJ's and Producers and often referred to as dubplates, very much used in the reggae, drum and bass and dubstep community.
A dubplate is an acetate disc – usually 10 inches in diameter – used in mastering studios for quality control and test recordings before proceeding with the final master, and subsequent pressing of the record to be mass-produced on vinyl.
The "dub" in dubplate is an allusion to the plate's use in "dubbing" or "doubling" the original version of a track.[1] The name dubplate also refers to an exclusive, 'one-off' acetate disc recording pioneered by reggae sound systems but also used by drum and bass and other electronic music producers, DJs and sound systems.These dubplates will often be either unreleased recordings (which may or may not end up being made available to the general public) or exclusive versions or remixes of existing recordings. They are often used as a market research tool to assess the probable sales of a tune once it is released, as they are far cheaper to produce than a pressed vinyl record.
The material of the disc is very soft as the groove is worn out little by little with every playback. After about fifty plays the loss in sound quality becomes noticeable. Vinyl dubplates are a recently developed format that allows exceptionally durable recordings to be made (lasting 90% as long as pressed vinyl records.
The benefits of short run vinyl cutting
The advantage to lathe cuts and Vinyl pressing is that you don't need a significant amount of money to get going and you can start of small and not be left with hundreds of records you cant shift yet.
You can also sell them at a premium even if you have a small following. Say you have 10 or 20 lathe cuts made, they are the only copies on vinyl anywhere in the world you can get creative by hand designing the artwork tailor-made for each buyer, individually signed or stamped. There are so many ways to be creative it is an exceptional product as each record is individually lathe cut.
With most of the vinyl pressing plants seemingly at capacity and records taking months to produce. Making short runs of lathe cut vinyl the way of getting records for your fans and promotional use quickly.
Brand New Record Presses
When CDs emerged in the mid-1980s, most of those aging LP presses ended up in landfills and warehouses. Fueled by the youth feeling nostalgic for something they had never experienced, vinyl is enjoying a stunning revival and, defying all predictions, has become more than just a passing fad. The Major labels rereleased their legacy acts on vinyl, and then they gave us Record Store Day.
The primary cause of all the delays is the renewed interest in vinyl records has meant that the old 1950s record presses have come back into service. The majority of the industry is still using these presses, and there has been no development until new vinyl presses have now come online from companies such as Newbilt
these guys have brought the first new presses in decades, the first 8 of the Newbilt lathes were installed in Jack Whites Third Man Pressing in Detroit, consisting of 2 x 7-inch vinyl presses and 6 x 12-inch vinyl presses.
There is also Viryl Technologies founded in 2015 by Chad Brown, Rob Brown, and James Hashmi. These guys have gone even further and manufactured a fully automated and semi-automatic record press as well as providing vital support for startups and the existing community.
Warm Tone Vinyl Press Fully Automated
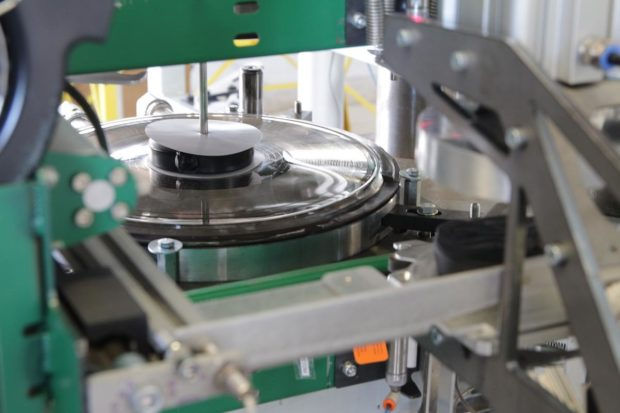
The first new record-pressing machines built in over 30 years are finally online. The brainchild of some Canadian R&D guys with a background designing MRI machines, the Warm Tone record press is everything that its vintage counterpart is not: safe, fast, fully automated, reliable, run by cloud-based software, and iOS-controlled. These $195,000 hi-tech machines, the new product of Toronto based company Viryl Technologies, are the record presses our 21st-century vinyl industry has been waiting for.
Unlike the old presses, a single worker can operate several Warm Tone units at once. Its unrivaled speed and efficiency leave the standard cycle time benchmarks in the dust, too: 20 seconds versus 35 seconds, which translates to three records per minute instead of only two. That's pretty good, but the actual product yield is even better than that. That's because the old school presses run at a 30 to 40 percent product loss due to everything from operator error to mechanical failure. To press a high-quality record, the vinyl "puck" is steam-heated up to 350 degrees Fahrenheit and water-cooled down to 50 degrees Fahrenheit in only 22 seconds. Product loss with the Warm Tone is a miserly one percent.
The Warm Tone is modular (making repairs a snap), mobile-friendly (manufacturing data is instantly relayed to smart devices through a custom interface), and has passed the most rigorous stress tests (24/7 operation is encouraged).
While the press churns away, Viryl Technology's proprietary quality-control software collects data from every vital point in the Warm Tone manufacturing process. The tool also allows the operator to make necessary tweaks in real time—from changing nozzle and steam pressure to adjusting flywheel trimming speed and vinyl blend—that can mean the difference between a successful run and a budget-breaking failure.
After much planning and infrastructure build-out, Hand Drawn Records, a 12-man indie label outside Dallas, has just flipped the switch on the first Warm Tones to enter the vinyl supply-side chain. Housed in the Hand Drawn Records Pressing plant in Addison, Texas, the two machines,
are currently running 18-hour shifts, and are on pace to churn out 1.8 million units in 2017.
Sony Japan Vinyl Pressing Plant
Almost thirty years after it left the vinyl market after they had introduced the now dwindling CD format. Sony will resume pressing again to deal with the growing demand for releases on record.
The factory south-west of Tokyo will churn out freshly pressed records from March 2018 but have heard no more information at this time.

Sony stopped making vinyl records in 1989 as consumers flocked to CDs and other emerging technology. Japan produced nearly 200m units a year in the mid-seventies, according to the country’s recording industry association.
Sony was a significant global player in the development of CDs, which have since taken a back seat to downloads and music streaming.
Vinyl Records are making a global comeback as it attracts not only older consumers but also the younger generations.

Japan’s sole record maker, Toyokasei, is struggling to keep up with the resurgence in vinyl demand, the Nikkei newspaper reported. That Sony is scrambling to find older engineers familiar with how to make records, it added.
The Sillitoe Audio Cutting Lathe
Tne newest and most advanced Vinyl Record Mastering lathe is soon to come onto the market, designed and built by the highly talented, creative individual James Sillitoe who has a real love for vinyl and his craft.
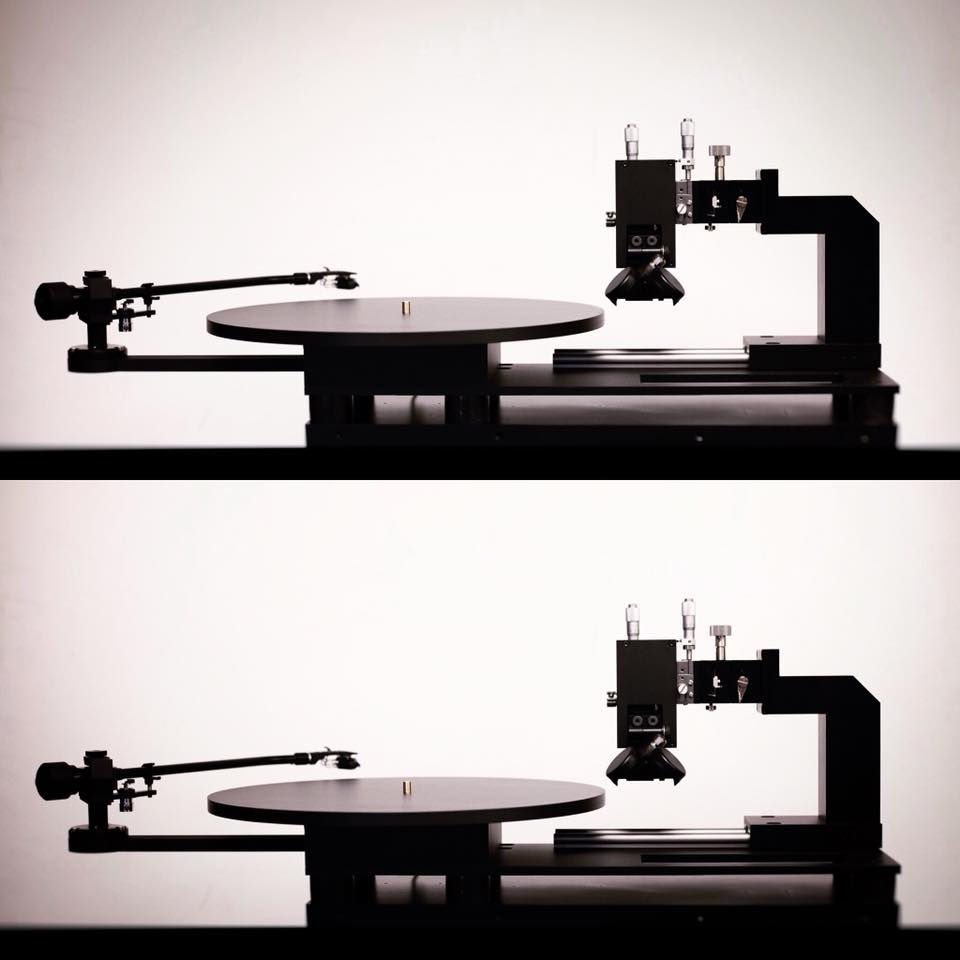
Desiged and built by James Sillitoe for Sillitoe Audio Technology
The lathe is almost ready for public release and the final tweeks are being made to this brilliantly designed and technically advanded lathe.
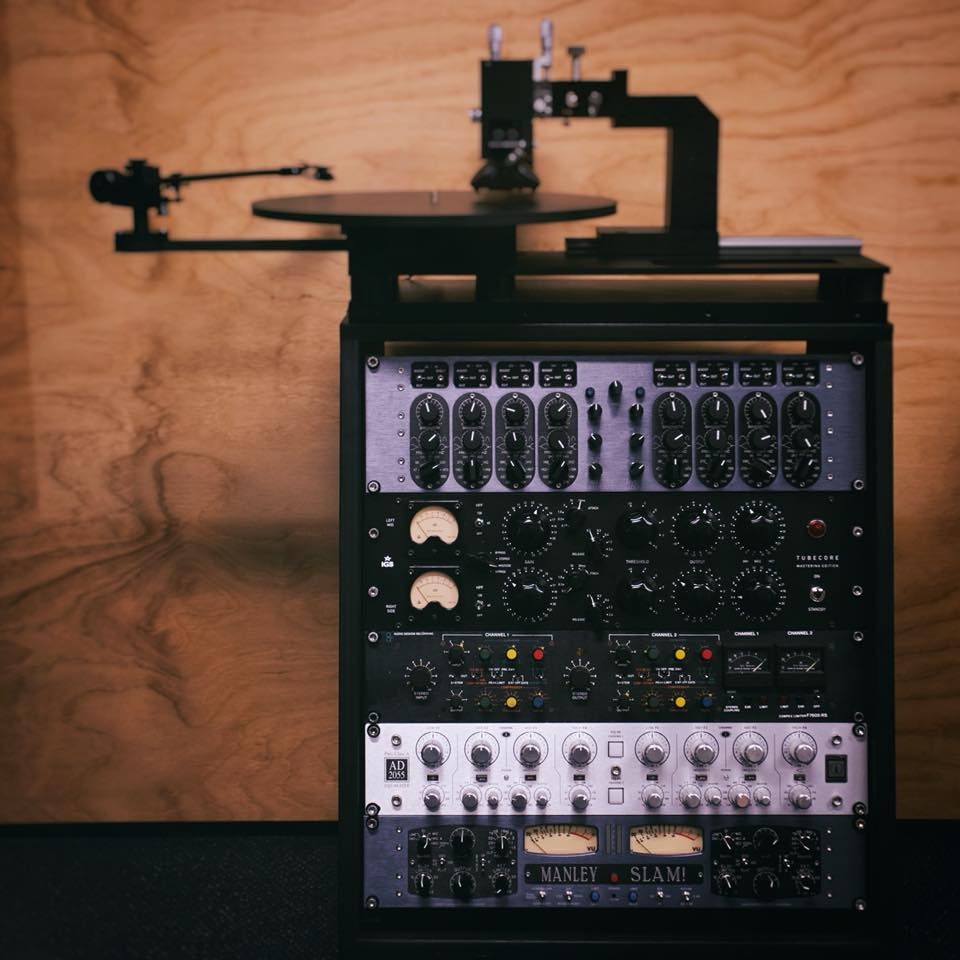
,
Comments